Concrete Leveling
Concrete floors and slabs, driveways, patios, pool decks and sidewalks can become uneven and break when the subsurface settles, change shape through freeze-thaw cycles, or when erosion moves the dirt and aggregates under the surface. In most cases, concrete settles below its original level, but in some cases, especially during severe freeze-thaw cycles, sections of concrete slabs can rise above their original alignment.
Concrete leveling can, in many cases, save existing concrete from permanent damage and the potential need for removal and replacement.
Uneven concrete floors, slabs, patios, and driveways present a number of problems:
- Uneven concrete surfaces increase the risk or tripping and injury
- Broken edges, especially in corners generally expand damage if not repaired
- Water accumulates in low spots, causing permanent damage to concrete
- Uneven concrete is unsightly and reduces property value
- Uneven surfaces make trimming, edging, shoveling and snow-blowing difficult and dangerous
3 ways to make concrete level:
- Depending on the circumstances, there are three primary ways to level concrete:
- Self-leveling Underlayment
- Mechanical leveling: Surface grinding
- Structural leveling: Mudjacking
1. Self-leveling underlayment: Above the surface
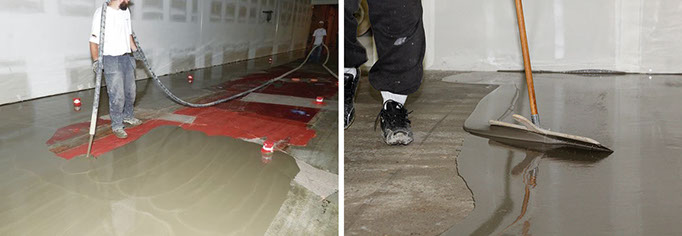
Self-leveling underlayment installation. Photos courtesy LATICRETE International.
- If the concrete is slightly out of level from side-to-side, corner-to-corner, or the concrete floor has low spots and there is little if any structural damage, The MJA Company may recommend an installation of “self-leveling underlayment.” Although the name implies that the material goes “under” something, self-leveling underlayment is a thin cementitious mortar that is installed on top of the uneven concrete floor.
- The mortar is poured onto the uneven surface and, because of it’s fluid properties, similar to pancake batter, it levels itself, much like water will always level itself, even in a tilted bowl.
- The downside to self-leveling mortars is their tendency to shrink and crack over time, especially if the floor is under stress. To strengthen the mortar, we may recommend a “sanded underlayment” which has a higher strength than conventional mortars.
- Self-leveling underlayments are not recommended for any floor with that is out of level by more than 3/16 inch. The MJA Company will inspect your floor and make the proper recommendations before a decision is made.
2. Mechanical leveling: Concrete Grinding
The most common problem we see for floors that are not level is when a section on concrete has risen above the level surface because of shifting below the concrete. This raised concrete can cause significant safety hazards, equipment damage and, over time, will be prone to further damage.
When this happens, the easiest and most economical fix is to restore the concrete to a level surface by grinding the high spots and creating and filling a saw cut to prevent further damage.
This method of concrete leveling is relatively inexpensive and works well on floors that have sections that have raised slightly above grade.
If the out-of-level section of concrete has raised too much, there is a risk of permanent damage to the concrete if it is ground beyond the top cementitious layer, exposing the aggregate. The top layer of a concrete floor protects the aggregate from loosening and deterioration.
Before recommending a grinding solution, The MJA Company will examine the concrete and determine which concrete leveling solution will best serve you.
3. Structural leveling: Mudjacking
If the concrete has sections that are tilted, you risk structural damage and injury from uneven surfaces. In these cases, concrete can be mechanically leveled.
In most cases, the sections that tilt down are raised through a process called mudjacking, in which special materials are injected through concrete and into the subsurface. This injection precisely raises the lower section to bring it level with the horizontal surface.
A series of small holes are drilled into the existing surface and the slab is restored to its proper position, with incremental lifts created by hydraulic pumping of custom-mixed limestone slurries or special liquid materials under the concrete. This leveling fills voids and restores concrete to a safe, level surface.
In very rare cases, sections that tilt above the level surface can be lowered by removing soil below the concrete, allowing the section to rest in place at a proper level. This type of repair is risky and expensive. It is likely that this type of problem will be better served by replacing the section(s) of concrete that are a concern.
Concrete leveling is usually less expensive than replacement, but always tricky business
Leveling concrete must be done by concrete professionals with experience in the structural mechanics of concrete, extensive knowledge of materials and processes, and an ability to determine the causes and proper options to complete the job safely and to assure years of restored service to the area.
Once a thorough inspection of the concrete is complete, The MJA Company will determine the safest, most cost-effective method of leveling your concrete.
Depending on the severity of displacement, cracks and chips may occur. The MJA Company will repair any damage and assure a clean, level surface.
Concrete leveling can be done in almost any weather at a savings of 50-70% of replacement.
As with every project, The MJA Company will discuss the best options and present a detailed, written estimate with our recommendations before we begin your concrete floor repair.